Used for decades in Europe, TimberHP by GO Lab brings wood fiber insulation to the Northern Forest
An architect and a chemist walk into a paper mill…
It’s an unlikely partnership in an unlikely corner of the world, but it doesn’t take long for TimberHP by GO Lab founders Matthew O’Malia and Joshua Henry to convey the relevance and potential of their new manufacturing venture in rural Maine.
The company, which launched in 2016, will manufacture insulation made from wood fiber as an environmentally-friendly and cost-competitive alternative to traditional fiberglass and foam insulation. Made from wood chips and waste from mills in Maine and the Northern Forest, the product, says O’Malia, solves two problems. One, it reduces embodied carbon in buildings which are responsible for 40 percent of our carbon footprint in the U.S. and, two, it creates a new, much needed market for low-grade wood.
A question in need of an answer.
An architect, leader in Passive House design, and the co-founder of GO Logic, O’Mailia found working with traditional insulation problematic. His firm was using three times the amount of insulation in construction to improve energy efficiency and lower the building’s operational carbon footprint, but most traditional insulations are carbon-intensive products made from fossil fuels.
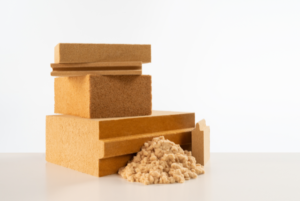
Timber HP Stack. Photo Courtesy of Go Lab.
“We were trading one environmental disaster for the next,” said Henry. “When you look at a job site before the exterior is put up, you’re looking at a giant Styrofoam™ cooler. We are always hearing ‘don’t put your coffee in a to-go cup or don’t use Styrofoam™ takeout containers,’ and then we’re wrapping entire buildings in the same materials.”
In 2016, O’Malia met Josh Henry, a chemist and professor at the University of Maine and enlisted Henry’s help in brainstorming solutions. “He was skeptical at first,” said O’Malia, “until he saw wood fiber insulation.”
Both methodical thinkers by profession, the pair went over the product, which has been used in Europe for decades, from every angle and kept returning to the same conclusions. The product is renewable, recyclable, non-toxic, and performance competitive with existing options. So, the only question was why wasn’t wood fiber insulation being made in North America?
Manufacturing in the Northern Forest.
The team dug in, building a business plan and continuing their due diligence on wood fiber insulation. They traveled to a factory in Germany to learn in detail how the product was made and realized that the main inputs for manufacturing—wood and energy—were less expensive in the U.S., meaning that not only was the product better for the environment, it would also be cost-competitive with existing mainstream insulations.
“It doesn’t make sense to put a layer of plastic around a building when you have a material that works just as well and is renewable, recyclable, non-toxic, AND cost competitive,” said Henry.
The real turning point came when, on a visit in Germany, they were presented with an opportunity to purchase lightly-used equipment. “The manufacturers in Germany gave us the right of first refusal,” said Henry. “There was a $40 million piece of equipment that we needed in there. We didn’t have the money, but we felt really strongly about this. I quit my job and we’ve been fundraising ever since.”
The company also purchased a recently closed paper mill in Madison, ME, and brought back some of the engineering and production staff who were familiar with the capabilities of the relatively modern facility.
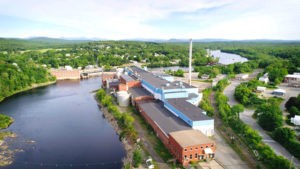
The Madison Mill in Maine; the new home of TimberHP. Photo courtesy of Go Lab.
“Not all manufacturing would make sense for Maine,” said Henry, “but there is a deep connection to the forest industry and an employment base that can make wood products.”
New England’s forest products industry has faced challenges over the past decade with increased competition from overseas and decreased demand for pulp paper products, leading to a significant loss of jobs in the region.
“Not a normal start up.”
With a business plan, facility, equipment, and a fledgling team lined up, the company began to fund raise in earnest. “We are not a normal start up,” said Henry. “A house is most people’s biggest investment. They don’t want something made in the garage. It has to be vetted and operating at the highest levels. That’s expensive – we had $4 million in engineering costs before we even got to financing – but true projects of social and environmental impact are going to be risky and they need that early stage capital.”
Janice St. Onge, president of the Flexible Capital Fund (the “Flex Fund”), and one of the early investors, agrees.
“Forests don’t stop at borders and neither do the connection points between families that have worked in the sawmills and forests for generations,” said St. Onge. “When we think about working, forested land and new markets for low-grade wood, we have to think regionally and invest in opportunity zones.”
The Flex Fund invested $200,000 into the more than $130 million endeavor. “It’s really meaningful money,” said Henry. “We launched in October 2020, mid-pandemic. Everyone told us they loved the idea but were waiting to see what would happen. The Flex Fund and others came through, helping us keep the lights on and keep moving forward. Janice agreed with us that the real risk was doing nothing to help rural economies in this environment.”
“We could have failed at any point,” said O’Malia, “but to have more sophisticated investors like Janice come in, to take a risk on us, was empowering. With every person that came in, we felt we had to make this happen no matter what.”
Hope for a sustainable future.
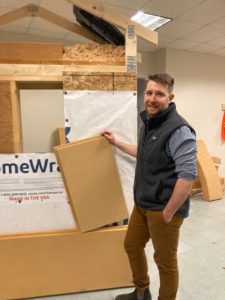
TimberHP by Go Lab founder Joshua Henry.
That same sense of loyalty and momentum extends to every person who has joined the TimberHP by GO Lab team. In addition to manufacturing a low-embodied carbon product and bringing jobs back to rural Maine, the company is committed to being an employer of choice, creating over 120 jobs in administration, sales and marketing, and production. These jobs will be offered at competitive wages, including health and retirement plans, paid time off, on job training, continuing education and more. Entry level production positions will start at $25 an hour.
“The money is one thing,” said Henry, “but the people who have been with us, who have stepped out on the ledge with us–love is not too strong a word. I love our team. I want to see this through for them to justify their belief in what we’ve put in front of them.”
O’Malia agrees. “We took on this ridiculously ambitious project to promote real change, and that other people have joined us gives me hope. There are people who are willing to change lanes to be part of something.”
“We can do more than we’re assigning ourselves,” he said. “The mood of this county is gloomy, it’s resigned. It is important to have a precedent that we can be better ecologically, economically, sustainably, and in terms of forest utilization and human health. We need wins out there. The state of Maine needs a win. Vermont needs a win. There are solutions with triple bottom lines that don’t mean you have to give something up. It can be better all around and there are indeed people who will take a leap to support change.”
About the Flexible Capital Fund
The Flexible Capital Fund, L3C is a Community Development Financial Institution (CDFI) and impact investment fund that provides flexible risk capital in the form of subordinated debt, revenue based financing (also known as royalty financing) and alternative equity structures, to growth-stage companies in Vermont and the region’s food systems, forest products, and clean technology sectors.